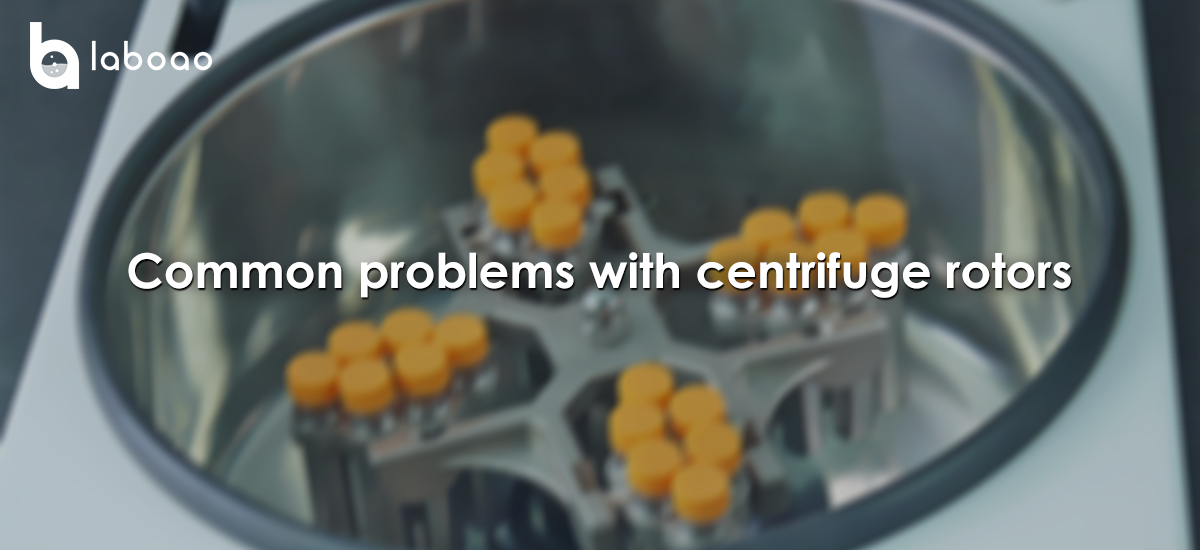
As the key part of laboratory centrifuge, the rotor is more strictly selected and manufactured, but it is inevitable that it will fail due to improper use and long-term stress damage.
1. Imbalance
Imbalance is the most common fault in various rotating machinery, and it also exists in laboratory centrifuges.
There are many reasons for rotor imbalance, such as unreasonable rotor structural design, machining quality deviation, assembly error, uneven material, poor dynamic balancing accuracy; changes in the relative position of the coupling during operation; rotor component defects, such as: corrosion, wear, uneven scaling and shedding of the medium during operation; the rotor is subjected to fatigue stress, causing partial damage and shedding of rotor parts (such as impellers, blades, belts, tie bars, etc.), resulting in fragments flying out, etc.
2. Misalignment
Rotor misalignment usually refers to the degree of inclination or offset between the axis line of the two adjacent rotors and the center line of the bearing.
Rotor misalignment can be divided into coupling misalignment and bearing misalignment. Coupling misalignment can be divided into three types: parallel misalignment, angular misalignment and parallel angular misalignment. When parallel misalignment occurs, the vibration frequency is twice the rotor power frequency. Angular misalignment adds a bending moment to the coupling in an attempt to reduce the angular deviation of the center lines of the two shafts.
Every time the shaft rotates one circle, the direction of the bending moment changes once. Therefore, angular misalignment increases the axial force of the rotor, causing the rotor to vibrate at the power frequency in the axial direction. Parallel angular misalignment is a combination of the above two situations, causing the rotor to vibrate radially and axially. Bearing misalignment actually reflects the deviation between the bearing seat elevation and the shaft center position.
Bearing misalignment redistributes the load of the shaft system. Bearings with heavy loads may experience high-order harmonic vibrations, and bearings with light loads are prone to instability, and the critical speed of the shaft system will also change.
3. Shaft bending and thermal bending
Shaft bending refers to the center line of the rotor being out of straight. Rotor bending is divided into two types: permanent bending and temporary bending.
Permanent bending of laboratory centrifuge rotors refers to the permanent bow shape of the rotor shaft. It is caused by unreasonable rotor structure, large manufacturing error, uneven material, improper long-term storage of the rotor, or failure to turn the rotor in time or improper turning when hot, poor thermal stability of the rotor, and increased natural bending of the shaft after long-term operation.
Temporary bending of the rotor refers to the large preload on the rotor, improper warm-up operation during startup, too fast speed increase, uneven thermal deformation of the shaft, etc.
Permanent bending and temporary bending of the rotor are two different faults, but the mechanism of their failure is the same. Whether the rotor is permanently bent or temporarily bent, it will produce a rotating vector exciting force similar to the mass eccentricity.